2205 duplex stainless steel is a typical representative of duplex stainless steel, in the duplex stainless steel application field dominates, is widely used in various industries, mainly including petrochemical Yao, marine and food. Its metallurgical organization of austenite and ferrite each accounted for half, about 40% ~ 60%, with ferritic stainless steel and austenitic stainless steel two materials performance. Because of its chemical composition contains Mo, it has a certain resistance to Cl- corrosion, the Hong Kong-Zhuhai-Macao Bridge, which was completed and opened to traffic in 2018, with a total length of about 55 km Yuan adopts the material is 2205 duplex stainless steel, effectively utilizing its superior corrosion resistance.
1 Test materials and methods
1.1 Test base material and test plate size The test base material is S32205 duplex stainless steel plate produced by Shanxi TISCO Stainless Steel Company Limited, with the size of 500 mm×300 mm×15 mm (length×width×thickness) and the quantity of 4 pieces.
1.2 Chemical composition and mechanical properties of parent material
Test with S32205 duplex stainless steel chemical composition is shown in Table 1, mechanical properties are shown in Table 2.

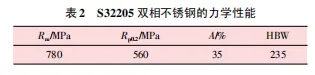
1.3 Proportion of parent material
2205 duplex stainless steel parent material (hot rolled plate) metallographic organization, as shown in Figure 1, the corrosive agent is FeCl3 aqueous solution, the organization consists of ferrite and austenite two-phase composition, the ratio of about 1:1, Figure 1, light gray for austenite, dark gray for ferrite, austenite is distributed in the ferrite matrix, the overall distribution of bars.
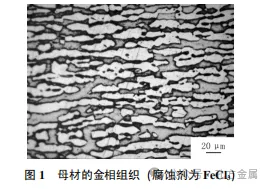
2 Experimental program
This study uses two test programs, delivery status are welding + heat treatment. The difference between the two programs is the welding method, the bottom welding are plasma welding, cover welding for TIG welding and SAW welding two kinds.
2.1 Option I
2.1.1 Test welding materials and equipment
Welding is done with stainless steel solid wire, U.S. Standard No. ER2209, the chemical composition of the wire is shown in Table 3, and the welding equipment used is the side beam double-gun P+T longitudinal seam welding system TETRIX522D-P, TETRIX 521 TIG, the power source is AC/DC 1000, and the welding position is flat welding.
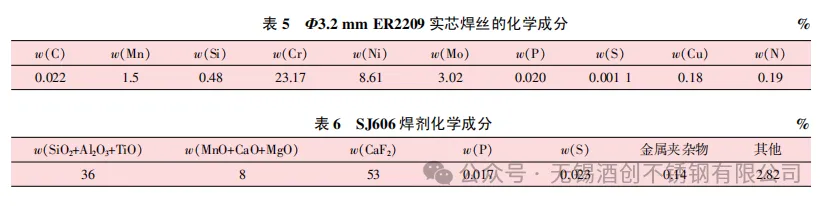
2.1.2 Process and inspection requirements
(1) Welding bevel form. Y-shaped bevel is used, the shape of the bevel is shown in Figure 2, and the distribution of the weld channel is shown in Figure 3.
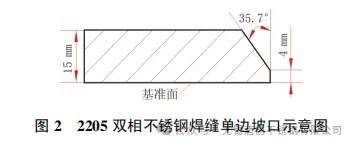
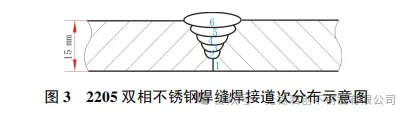
(2) Welding method, process requirements and parameters. Welding method: PAW without filler wire bottom welding + TIG filler wire cover welding; welding and shielding gas are pure Ar. Welding process requirements: use angle grinder or acetone to clean up oil and rust within 30 mm range of the weld and both sides before welding and between layers; use small welding energy for multi-layer and multi-channel welding; strictly control the temperature between layers ≤ 100°C. Welding process parameters are shown in Table 4.
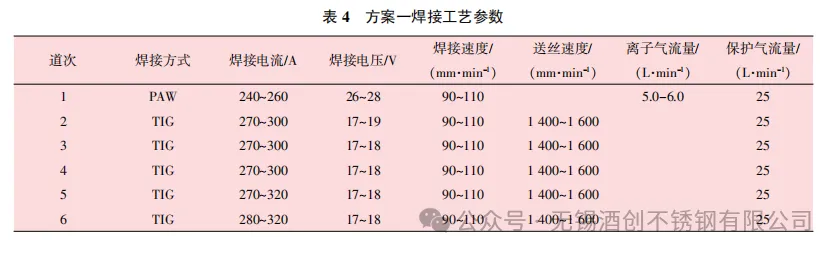
(3) Welding seam inspection. After completion of welding, the weld is visually inspected for appearance, size and RT real-time imaging. The result of visual appearance inspection meets the requirements of standard NB/T 47013.7; ray inspection is in accordance with the requirements of standard NB/T 47013.2, and no biting edge, porosity is found. There is no fusion, cracks and other defects, and the quality meets the requirements of Grade Ⅰ.
(4) Heat treatment. After the weld is detected without defects, it is heat-treated at a temperature of 1050 °C, a holding time of 30 min, and the cooling method is water-cooled.
2.2 Option II
2.2.1 Test welding materials and equipment
Submerged arc welding uses stainless steel solid wire, grade ER2209, specifications 10~60 mesh. The chemical compositions of the wire and flux are shown in Table 5 and Table 6 respectively, and the welding equipment uses the automatic double-gun P+S longitudinal seam welding system for the side beam. The welding position is flat welding.
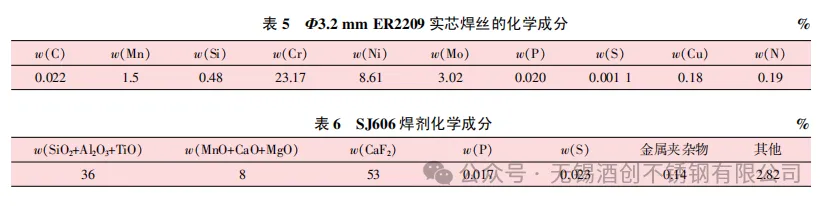
2.2.2 Process and inspection requirements
(1) Welding bevel form. Y-shape bevel is adopted, with 4 welding passes, 1 pass for PAW priming and 3 passes for SAW filling and covering.
(2) Welding method, process requirements and parameters. Welding method adopts PAW bottom welding + SAW cover welding, PAW ion gas and shielding gas are pure Ar, the specific process parameters are shown in Table 7, and the process requirements are the same as TIG cover welding. (3) The appearance of weld, non-destructive testing and heat treatment process requirements are the same as Program 1.
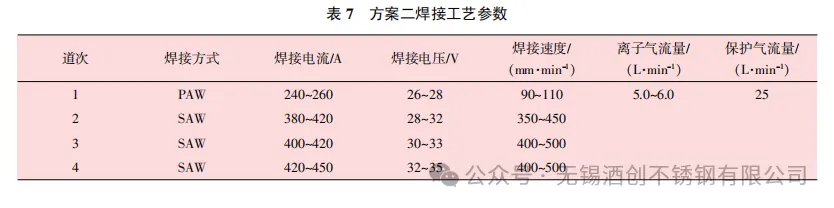
3 Physical and chemical properties of welded joints
The physical and chemical properties of the weld are examined by tensile, bending, metallographic, and pitting tests. According to ASME Boiler and Pressure Vessel Code IX "Welding and brazing process, welders, brazers, welding and brazing operators assessment standards" requirements for sampling and testing. The test is conducted by 30 t electronic tensile testing machine produced by Steel Research Naktronic Inspection Technology Co., Ltd. for tensile and bending test; pitting test is based on standard ASTM G48.
3.1 Mechanical properties
3.1.1 Welded seam transverse tensile test stretching
Specimen dimensions as shown in Figure 4 Yuan length 450 mm, width 50 mm, thickness 15 mm, the specimen requires internal and external weld residual height mechanical grinding.
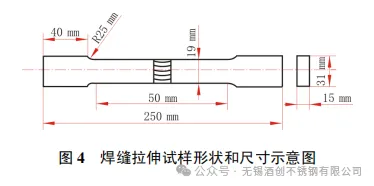
The specimens were tested at a loading rate of 5 mm/min and a load of 10 kN in accordance with ASTM A370, and the results of the mechanical properties are shown in Table 8.
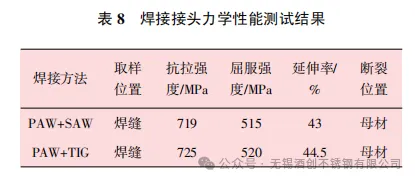
According to the American Standard ASME Boiler and Pressure Vessel Code IX "Leaf Welding and Brazing Process, Welders, Brazers, Welding and Brazing Operators Assessment Standards", QW-153 tensile test qualification criteria: the tensile strength of the specimen is not less than the minimum tensile strength of the parent material, according to the table QW / QB-422 can be understood, the minimum value of tensile strength of the parent material for the provisions of 655 MPa.
From Table 8 test data can be seen: argon arc welding and submerged arc welding weld tensile strength test value of 725 MPa and 719 MPa are higher than the base material requirements of the minimum tensile strength of 655 MPa, yield strength is higher than the base material standard value of 485 MPa, elongation is greater than the base material requirements of the minimum value of 25%, the test is qualified, the tensile specimen fracture position in the base material, indicating that the weld performance is good.
3.1.2 Bending test
The thickness of the test plate is 15 mm, when doing the bending test instead of the side bending test face bending and back bending. Specimen width for the original thickness of the base material 15 mm, specimen thickness of 10 mm, length 160 mm. specimen requirements for internal and external weld height of mechanical grinding. The shape and size of the weld bending specimen is shown in Figure 5.
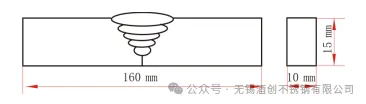
Test conditions: bending diameter of 40 mm, bending angle of 180 °. Test implementation standard ASTM A370. Test implementation standard ASTM A370. 10 times magnification under the microscope after the test to observe the outer surface of the weld without cracks, argon arc welding and submerged arc welding cover two welding process bending test are qualified.
3.2 Metallographic observation
3.2.1 Comparison of metallographic organization of welded joint weld zone
Weld metallographic test is mainly to test the organization of welded joints and the ratio of austenite and ferrite phases. Welded joints weld zone metallographic organization shown in Figure 6, Figure 6 (a) for the argon arc welding weld zone organization, Figure 6 (b) for the submerged arc welding weld zone organization, corrosion fluid for aqua regia. As can be seen from Figure 6, submerged arc welding weld organization is more directional, the whole was dendritic crystal, argon arc welding weld also exists dendritic crystal, directionality than submerged arc welding is not obvious.
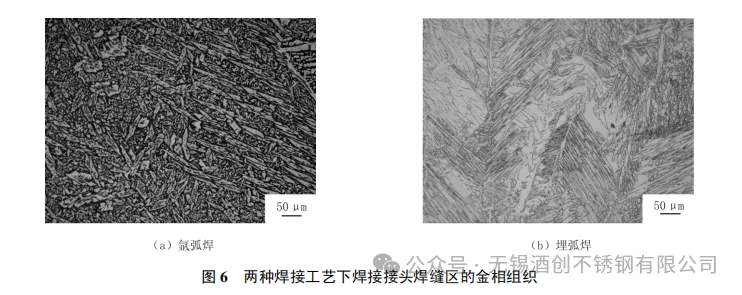
3.2.2 Comparison of metallographic organization of heat affected zone of welded joints
Welded joints under the two welding processes heat-affected zone metallurgical organization shown in Figure 7, Figure 7 (a) for argon arc welding cover heat-affected zone organization, Figure 7 (b) for the submerged arc welding heat-affected zone organization, corrosion fluid for aqua regia. As can be seen from Figure 7, submerged arc welding heat-affected zone organization was continuous band distribution, argon arc welding heat-affected zone organization was intermittent strip distribution; welded joints in the heat-affected zone of austenite and ferrite two-phase proportions of each accounted for about 50%.
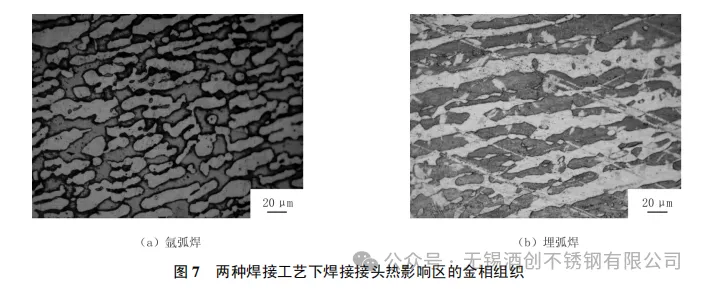
3.2.3 Comparison of metallographic organization of base material area of welded joints
Metallographic organization of the base material area of the welded joints under the two welding processes as shown in Figure 8, Figure 8 (a) for the argon arc welding cover base material area organization, Figure 8 (b) for the submerged arc welding base material area organization, the corrosion fluid is aqua regia. The two charts show the center of the weld and the center of the position of the parent material of the metallurgical organization, but due to the submerged arc welding heat input is greater, Figure 8 (a) organization close to the parent material, was intermittent stripe distribution; affected by the heat input, Figure 8 (b) organization similar to the organization of the heat-affected zone, was a continuous band distribution; weld two-phase ratio are to meet the requirements of the two phases of the ratio of argon arc welding accounted for about 50%, the submerged arc welding ferrite content is slightly higher, the submerged arc welding. According to ASTM E562 standard can be seen, the ferrite content of about 55%.
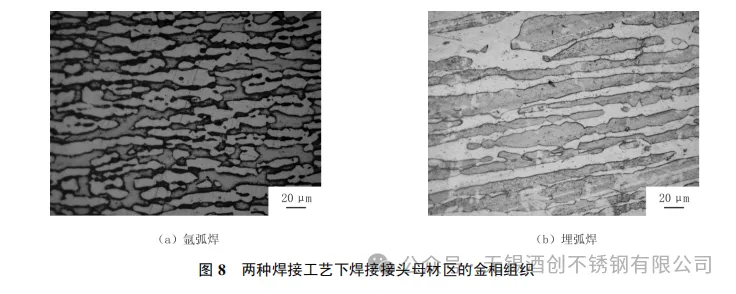
3.3 Corrosion resistance test
In this study, the weld corrosion resistance test is mainly to detect its pitting resistance, the test method is ferric chloride pitting corrosion test, the implementation of the standard ASTM G48, the test temperature of 30 ° C. The test method is to detect the corrosion resistance of the weld, the test method is ferric chloride pitting corrosion test.
Argon arc welding cover weld pitting test: specimen size of 25.05 mm × 15.11 mm × 2.45 mm, specimen surface area of 953.795 mm²; the specimen will be ground and cleaned into the 6% ferric chloride solution corrosion for 72 h, before the test weighed 7,231.2 mg, weighing after the test 7,229.8 mg, corrosion rate of 0.49 g/m²/ 24h; after the test 20 times magnification without visible pitting phenomenon. 24h; after the test, there is no visible pitting phenomenon on the surface of the specimen when magnified 20 times.
Submerged arc welding cover weld pitting test: specimen size of 25.12 mm × 15.04 mm × 2.19 mm, specimen surface area of 931.510 4 mm²; the specimen will be ground and cleaned into the 6% ferric chloride solution corrosion for 72 h, weighed before the test for 6452.7 mg, weighed after the test for 6 450.9 mg, the corrosion rate 0.64 g /m²/24h; after the test, there was no visible pitting corrosion on the surface of the specimen when magnified 20 times.
According to the results of the two groups of pitting test can be seen, argon arc welding cover weld pitting resistance is better than the submerged arc welding cover weld pitting resistance.
By comparing the physical and chemical properties and metallurgical organization of the weld between TIG welding and SAW welding, it is found that the organization and physical and chemical properties of TIG cover weld are better than that of SAW cover process, but the production efficiency of SAW is more than 3 times higher than that of TIG, so the welding process can be selected by considering the application working conditions and production efficiency. If the application conditions are harsh, the TIG process is preferred; if the requirements for the use of the environment are not high, the SAW process can be selected in consideration of production efficiency.