Synopsis:MX3D, a large-scale 3D metal printing company, has successfully produced a duplex stainless steel structural connector by designing it in collaboration with engineers from one of Japan's largest architectural, engineering and construction companies (Takenaka).
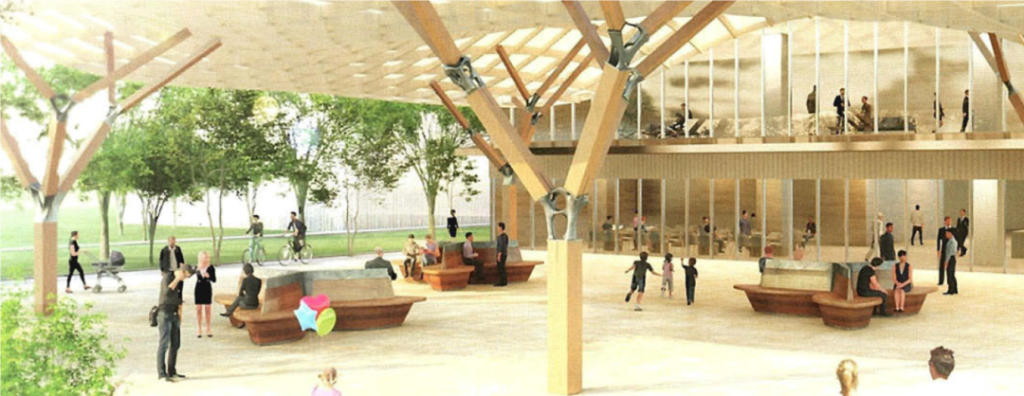
Figure 1 Artistic trends in 3D printed steel connectors available for use in public buildings
This project demonstrates progress in the production of highly customized engineered steel connectors using robotic 3D metal printing, known as Wire Arc Additive Manufacturing (WAAM) technology. Destructive and non-destructive testing was carried out on a range of printed duplex stainless steel connectors, which demonstrated strong and consistent mechanical and material properties. Successful testing is a key step towards certification of the structural connectors, which the parties intend to use in innovative construction projects.
Innovative infrastructure
In 2019, Takenaka and MX3D launched a collaborative project to explore the possibilities of robotic WAAM technology - producing large customized steel connectors for the infrastructure industry. The goal of the project is to automate the design and manufacture of complex connectors for large structures in the construction industry. Due to the increased complexity of structures, skilled labor is scarce and speed of construction is key, hence the need for innovation. After the first successful prototype production of the connectors, the collaboration focused on mechanical and material property testing, which is a key requirement for market acceptance.
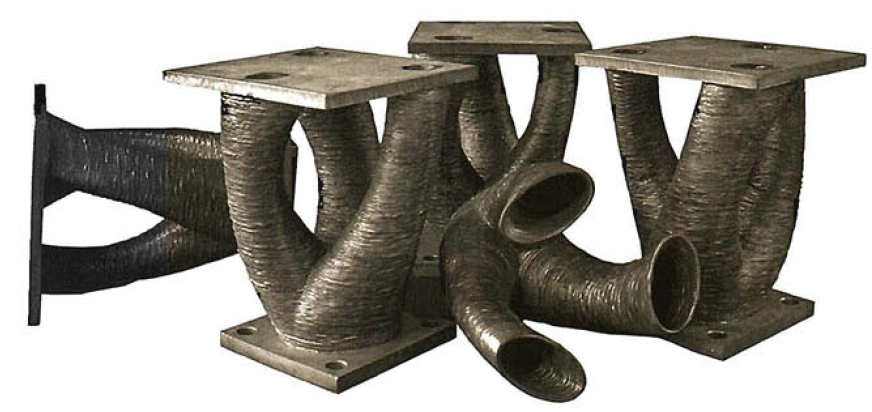
Figure 2 3D printed duplex stainless steel connector kit
rigorous testing
The results of destructive testing of a series of printed structural connectors showed strong and stable mechanical and material properties, paving the way for certification of the structural connectors. The results of tensile, fatigue and flexural tests on the connectors were convincing, and CT scans showed that the internal structure was dense and solid. Furthermore, the compressive damage test showed that the mortar filling had a significant effect on the flexural and ultimate strength. The strength of the 4mm thick connectors using mortar filling was roughly the same as that of the 8mm thick connectors (2.2kN vs. 2.3kN, respectively), which reduces the amount of 50% of material required and is more conducive to the morphological freedom of 3D metal printing. The material properties and mechanical tests met the expected standards and stability, establishing the relevance of robotic 3D printing to industry.Fig. 3 Deformation predicted by the analysis of connectors vs. actual
Duplex stainless steel: the ideal material
The initial samples of the connector series were printed in duplex stainless steel. This alloy is known for its good mechanical properties and excellent corrosion resistance, making it an ideal material for structural applications. Concrete-filled hollow steel structures offer efficient and cost-effective safety, with an internal concrete core that delays or prevents localized buckling and other steel sections that are subjected to bending and tensile forces.
Takenaka researchers used information from physical tests on material samples to generate an FE simulation model to evaluate the mechanical properties of the joints, and then tested the properties of the actual joints subjected to compressive loads against these evaluations, and the simulation results were very close to the properties of the mechanical tests. In addition, the tensile strength tests showed a highly consistent pattern, making this technique one of the tools architects and engineers need. The full study will be published soon. With the successful fabrication of optimized printed structural steel connectors and strong test results, the participating partners intend to complete larger models in real building projects.
Starting to use AM (3D printing) technology in the construction industry
Closed-loop digital design loops are a key element in the architectural, engineering, and construction industries, and MX3D's robotic WAAM technology for producing such joints provides full digital control of design, production, schedule, cost, and logistical efficiencies, as well as integration with BIM (Building Information Modeling) applications.MX3D's MetalXL application now allows manufacturers to quickly start large-scale 3D metal printing applications in their own facilities. their own factories to quickly turn on large-scale 3D metal printing applications.
The results of this research program's robust mechanical and material property evaluation confirm the relevance of robotic 3D metal printing to the architecture, engineering and construction industry, and pioneers a new generation of structural connectors for the AEC (architecture) industry.