Duplex stainless steel is composed of austenite and ferrite two phases, when the ratio of the two phases is about 50%, duplex stainless steel will austenitic stainless steel with excellent toughness and weldability and ferrite stainless steel with all the higher strength and resistance to chloride stress corrosion combined together, so that both austenitic stainless steel and ferritic stainless steel advantages.
Duplex Stainless Steel 2205 is produced by AvestaPolarit in Sweden under the commercial grade 2205CodePlusTow, which has been incorporated into ASTM and ASME's A240 and A480, and UNS No. S32205, and belongs to the second generation of duplex stainless steels. 2205CodePlusTow is differentiated from its counterpart, UNS No. S31803, in that it increases the lower limit of nitrogen content and passes the harmful metal phase precipitation test. 2205CodePlusTow has higher strength and corrosion resistance, and passes the harmful metal phase separation test. Duplex stainless steel 2205 is different, it improves the lower limit of nitrogen content, and through the harmful metal phase precipitation test. 2205CodePlusTow has higher strength, corrosion resistance and post weld metallurgical stability, welded joints are easy to obtain a balanced two-phase organization, high nitrogen content is more effective in suppressing the precipitation of harmful metal phases, which is very favorable to welding.
Since the early 1980s, China has been exploring in depth an outstanding performance stainless steel material called 00Cr22Ni5Mo3N, which is chemically similar to SAF2205, a unique duplex stainless steel that combines the dual properties of ferritic and austenitic. This material is known for its remarkable high strength, with a yield strength that is more than twice that of ordinary austenitic stainless steels, while it maintains an excellent plastic deformation capacity, ensuring the material's flexibility during processing.
The impact toughness of 00Cr22Ni5Mo3N duplex stainless steel performs particularly well at low temperatures, which makes its use in extreme conditions possible. It exhibits excellent resistance to many forms of corrosion, such as stress corrosion, intergranular corrosion, pitting and crevice corrosion, thanks to its unique microstructure and compositional design. Compared with conventional austenitic stainless steels, the material has better thermal conductivity and a lower coefficient of linear expansion, properties that not only optimize its heat treatment process, but also improve weldability and reduce the tendency to thermal cracking. In addition, 00Cr22Ni5Mo3N duplex stainless steel in the nickel content is relatively low, which not only reduces the production cost, but also makes the material more competitive price in the market. These advantages make it shine in the chemical industry, petroleum energy, marine engineering and other industries, and become one of the most popular and widely used duplex stainless steel in these fields, showing its great potential and wide applicability in industrial applications.
Welding control and post weld inspection play a pivotal role in the process of ensuring the quality and performance of duplex stainless steel welds. In order to achieve this goal, in the welding control link, the welding parameters must be precisely managed, including welding speed, current strength and voltage level, in order to maintain the smoothness of the welding process and ensure the consistency and quality of the weld. In addition, the careful selection of welding technology and welding materials should not be underestimated, as they are directly related to the mechanical strength and corrosion resistance of the welded joint.
This process emphasizes the importance of precision in parameter control and material selection, which complement each other and together determine the reliability and service life of the welded structure. By carefully regulating welding speed, current and voltage, welding defects such as cracks, porosity and unfusion can be effectively prevented, thus improving the integrity and performance of the welded joint. At the same time, the selection of welding materials that match the base material can ensure that the welded area and the base material have similar mechanical properties and corrosion resistance, which further improves the stability and durability of the entire welded structure. In short, the welding process of duplex stainless steel requires comprehensive consideration of the control of welding parameters and material selection, through scientific and reasonable welding methods, to achieve the high strength of welded joints and excellent corrosion resistance, to ensure that the welded structure in the complex environment of long-term safe operation.
Duplex stainless steel in solid solution at room temperature in austenite and ferrite accounted for about half (duplex stainless steel 2205 ferrite content should be 30% ~ 55%, the typical value of 45% or so), both two-phase organizational characteristics, see Figure 1. it retains the ferritic stainless steel thermal conductivity, coefficient of linear expansion is small, resistance to pitting, crevice and chloride stress corrosion; and has a good toughness, good brittle transition temperature is low, resistance to intergranular corrosion. Austenitic stainless steel toughness, brittle transition temperature is low, resistance to intergranular corrosion, mechanical properties and welding performance advantages.
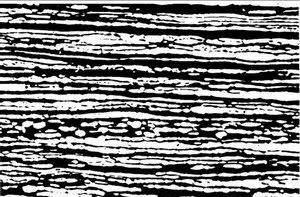
Figure 1 Typical microstructure of 2205DSS plate
I. Performance characteristics of duplex stainless steel
The outstanding performance is high yield strength and stress corrosion resistance. Duplex stainless steel than austenitic stainless steel yield strength is nearly one times higher than the same pressure level conditions, you can save material. Than the austenitic stainless steel linear coefficient of thermal expansion is low, and low carbon steel close. Make duplex stainless steel and carbon steel connection is more appropriate, which has great engineering significance. Forging and cold stamping molding is not as good as austenitic stainless steel. Duplex stainless steel 2205 mechanical properties are shown in Table 2.
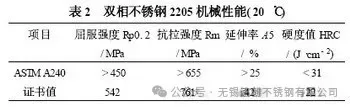
II. Duplex stainless steel weldability
Duplex stainless steel 2205 has good weldability, welding cold cracks and hot crack sensitivity are small. Usually no preheating before welding, no heat treatment after welding. Due to the high nitrogen content, the heat affected zone of the single-phase ferrite tendency is small, when the welding material selection is reasonable, welding line energy control is appropriate, the welded joints have a good overall performance.
1. Thermal cracks
Thermal cracking sensitivity is much smaller than austenitic stainless steel. This is because the nickel content is not high, easy to form low melting point eutectic impurities are very few, not easy to produce low melting point liquid film. In addition, there is no danger of rapid growth of grains at high temperatures.
2. Embrittlement in the heat affected zone
The main problem of duplex stainless steel welding is not in the weld, but in the heat-affected zone. Because in the welding thermal cycle, the heat-affected zone in the fast-cooling non-equilibrium state, always retain more ferrite after cooling, thus increasing the corrosion tendency and hydrogen cracking (embrittlement) sensitivity.
3. Ferrite 475 ℃ embrittlement
Duplex stainless steel containing 50% or so ferrite, the same also exists 475 ℃ embrittlement, but not as sensitive as ferritic stainless steel.
III. Welding metallurgy of duplex stainless steel
Duplex stainless steel welding process, under the action of thermal cycling, the weld metal and the heat affected zone of the organization of a series of changes. At high temperatures, all the duplex stainless steel metallurgical organization is composed of ferrite, austenite is precipitated in the cooling process. The amount of austenite precipitation is affected by many factors.
1. Phase ratio requirements
The core of duplex stainless steel welding technology is to maintain a balanced ratio of ferrite and austenite in the welded joint, which is directly related to the mechanical properties and corrosion resistance of the material. Ideal welded joints should show nearly equal amounts of ferrite and austenite, so that the structure can maximize the reproduction of the excellent characteristics of the parent material. Especially in 2205 duplex stainless steel, the ideal range of ferrite content is around 45%, this ratio can ensure that the material's comprehensive performance is optimized. Once the ferrite content deviates from this ideal range, whether it is low (below 25%) or high (more than 75%), the material performance will be adversely affected. Too low a ferrite content will weaken the strength of the material and reduce its ability to resist stress corrosion cracking; while too high a ferrite content will lead to a decrease in corrosion resistance and impact toughness, both of which are important indicators of material performance. Therefore, precise control of ferrite content during welding to keep it within the ideal range is the key to ensuring the performance of duplex stainless steel welded joints. The challenge of duplex stainless steel welding is to find a fine balance, that is, by controlling the welding process parameters, so that the ratio of ferrite and austenite in the welded joints is close to 50:50, especially for 2205 duplex stainless steel, ferrite content is maintained at about 45%, to ensure that the welded joints have mechanical properties and corrosion resistance comparable to that of the parent material, and at the same time avoiding too low or too high The ferrite content of the material properties of the negative impact.
2. Phase ratio influencing factors
The equilibrium of ferrite and austenite in welded joints is influenced both by the content of alloying elements in the steel and by the filler metal, welding heat cycle, and shielding gas.
2.1 Influence of alloying elements
Research has shown that nitrogen in the base material plays a crucial role. It is highly effective in ensuring the formation of sufficient austenite organization in the weld zone and heat affected zone. Similar to nickel, nitrogen is a key element in promoting austenite formation and expanding its presence, but nitrogen far exceeds nickel in this ability. Especially at high temperatures, nitrogen is more effective than nickel in stabilizing the austenite structure, preventing the emergence of a single ferrite phase after welding, and at the same time inhibiting the precipitation of unfavorable metallic phases, thus enhancing the overall performance of the weld material.
In the welding process of duplex stainless steel, controlling the microstructure of the weld metal is essential to ensure the material properties. When self-fusion welding is used or the filler metal is consistent with the composition of the base metal, thermal cycling in the weld zone can lead to a significant increase in the ferrite phase and sometimes even the formation of a pure ferrite structure, which may affect the mechanical properties and corrosion resistance of the weld. In order to effectively control the excessive generation of ferrite, modern welding trends favor the use of weld metals with austenite as the dominant phase. The two main ways to achieve this are to increase the nickel content or to add nitrogen. By boosting the percentage of nickel in the weld material, typically 21 TP3T to 41 TP3T above the base metal, the formation of the austenite phase can be promoted. For example, for welding 2205 duplex stainless steel, the nickel content in the filler metal can be as high as 81 TP3T to 101 TP3T. However, the use of nitrogen-containing filler materials has proven to be more effective than simply increasing the nickel content. Both nickel and nitrogen can promote the formation of austenite phase and increase its stability, but the addition of nitrogen can not only inhibit the precipitation of intermetallic phases, but also significantly improve the strength and corrosion resistance of the weld metal. Therefore, in the welding of duplex stainless steel, the reasonable addition of nitrogen is an effective strategy to optimize the weld microstructure and enhance the overall performance of the material. This practice through the fine control of the phase composition of the weld metal, not only to avoid the excessive generation of ferrite, but also through the enhancement of the stability of the austenite phase, to further enhance the comprehensive performance of welded joints.
For duplex stainless steel 2205, tungsten arc welding selection Sandvik22.8.3.L (ER2209) wire, electrode arc welding selection Avesta2205AC/DC electrode is to meet the requirements of the welding material. Duplex stainless steel 2205 and welding materials in the alloying elements of these characteristics, for the welding process parameters, namely, the choice of welding line energy provides a certain range, which is very favorable to the welding.
2.2 Effects of the thermal cycle
Duplex stainless steel welding process is unique, the key lies in the welding process of thermal cycling can significantly affect the microstructure of the welded joint, this characteristic is not only reflected in the weld region, but also covers the heat affected zone. During the welding process, phase changes occur within the material, which are directly related to the performance of the welded joint. In order to optimize this process, the use of multi-layer, multi-pass welding technology has proven to be an effective strategy. The implementation of this technique allows the subsequent welding paths to perform a heat treatment-like effect on the previous weld, promoting the transformation of the original ferrite phase in the weld metal to the austenite phase, forming a composite phase structure dominated by austenite. At the same time, with the weld adjacent to the heat-affected zone, the proportion of austenite phase will also be increased, which helps to refine the ferrite grain, inhibit the precipitation of carbides and nitrides in the grain boundaries and intragranular, thus comprehensively improving the microstructure and overall performance of the welded joints, and achieving better mechanical and corrosion resistance properties.
2.3 Influence of process parameters
Welding process parameters, especially welding line energy, are critical to the microstructure equilibrium of duplex stainless steel. In the high temperature state, duplex stainless steel presents a ferrite structure of 100%. If the wire energy is set too low during welding, the cooling rate in the heat affected zone will be abnormally fast, resulting in insufficient time for the austenite phase to form, and as a result, the ferrite phase is retained in excess at room temperature, which is not the ideal state. On the other hand, if the wire energy is set too high, the cooling process becomes too slow, and although this can lead to sufficient austenite formation, it can also lead to abnormal growth of ferrite grains in the heat-affected zone and precipitation of harmful metal compounds such as σ-phase, which can significantly reduce the toughness of the welded joints and lead to embrittlement problems.
In order to avoid these situations, the best measures are to control the welding line energy and interlayer temperature and to use filler metals.
2.4 Effect of protective gases
Tungsten argon arc welding, can be added in the argon 2% nitrogen, to prevent the weld surface due to diffusion and loss of nitrogen, contributing to the balance of ferrite and austenite.
IV. Duplex stainless steel welding process
Welding process should usually specify the welding line energy range and the highest interlayer temperature. It is usually recommended that the wire energy of 110 ~ 215kJ / mm, the interlayer temperature control in the 150 ℃ below.
Preheating is not normally required, but should be carried out appropriately if the workpiece is wet or if the workpiece temperature is below 5°C prior to welding. There are also fabrications with large constraints and especially thick-walled structures where preheating up to 100°C is advantageous, and further details on preheating should be consulted. The oxyacetylene flame should not come into direct contact with the surface of the material and there should be no excessive hot spots.
The use of 99.99% argon inert gas protection, manual tungsten arc welding bottoming welding includes the following process steps: 1) choose 300 manual / tig welding machine, power supply polarity for DC positive connection, pool shielding gas for 99.99% argon, flow rate of 10-18 liters / min, back shielding gas for 99.99% argon, argon arc welding wire for AWSA5.9: ER2209, tungsten Thorium tungsten pole Φ2.4, ANSI/AWSA5.12-92, the welding position is fixed horizontally, the wall thickness is 8-10 mm, the joint form is butt V interface, the bevel angle of 60 ° ± 5 °, blunt edge of 0-1.5 mm, the gap is 3-5 mm; (2) will be set up a good level of workpiece fixed in the weld frame, sealing the mouth of the tube to leave the inlet and outlet only, argon gas in the tube for the back of the protective gas Gas 3-5 minutes, the gas flow rate of 5-10 liters / min; (3) licensed welders bottoming welding, the current is 70-90 amps, the voltage is 11-13 volts, the welding speed of 30-50 mm / min, continue to pass the back of the protective gas.
In the welding process, controlling the interlayer temperature and welding line energy is the key to ensure the quality of the joint. The two synergistic effects directly affect the cooling rate, which in turn affects the corrosion resistance and impact toughness of the joint. If the interlayer temperature or arc energy is too high, the joint performance will be impaired. Therefore, it is critical to balance the two to ensure that the joint performance is optimized. Lowering the interlayer temperature is necessary when the weld line energy is out of the appropriate range. The maximum permissible interlayer temperature should be specified in the Welding Procedure Specification (WPS), which should normally be below 150°C. The temperature should be set at a maximum of 150°C for each start. To monitor the interlayer temperature, a contact thermocouple should be used to measure it immediately before starting a new weld pass and at recommended pause points. Ensure that the temperature of the weld area has dropped below the interlayer temperature before re-welding. Monitoring of the interlayer temperature should not be limited to just before starting a new weld pass, but should be done at every time interval throughout the weld process to keep track of temperature changes in real time and to ensure weld quality.
The GTAW welding method method is usually specified for undercut weld passes, and the following table shows the recommended parameters.
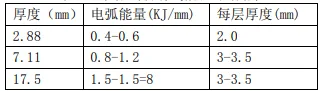
As a general guideline, the second layer of cold weld passes requires a lower weld line energy than the base weld pass. The second layer of cold weld pass over the surface of the root pass should be ground smooth if required and scrubbed with a stainless steel brush. However, grinding is hardly ever required. The GTAW welding method is usually used. The interlayer temperature must be controlled as previously described, and adjustment of the weld pool may be necessary to ensure that the weld pool is tapped. Tapping can be achieved by tapping the weld pool against the side wall. Oscillation must be minimized. Single-pass or split-pass welding techniques can be used within the limits of arc energy and joint bevel form requirements.

Joint filler layer To avoid oxidation of the successive root passes during repeated heating, backside argon gas protection should be applied prior to the application of the tube and the molten metal thickness up to 12 mm plate single side welding. For the first 5mm thickness of welded joints, the weld sequence should be maintained in a uniform manner. Throughout the joint welding process, the interlayer temperature and line energy should be controlled.
Filling of joints by manual electrode arc welding (SMAW) requires a proper electrode drying process, especially protection against moisture absorption. Welding electrodes in unopened packages, vacuum containers, or from holding tanks with a minimum temperature of 150 degrees Celsius can be used directly. The quantity of electrodes to be dispensed should be sufficient for a 4 to 5 hour production run, the quantity of electrodes to be dispensed from the vacuum packaging should be sufficient for a production run of 8 to 10 hours, and the electrodes should be stored in the thermowells during use. In any case, the welding consumables manufacturer's instructions for the use of special types of welding flux paste shall be observed. The welding technique should be controlled according to the electrode, avoiding large pronounced oscillations and high heat input, and avoiding contact with the arc. The electrode should be operated within the current range recommended by the manufacturer, typical parameters of which can be found in Table 6.
GMAW filler Ф1.0 and 1.2 mm diameter wires can be used for welding super duplex stainless steels. The use of multi-layer, multi-pass interlayer passes with minimal oscillation and controlled arc energy is advocated for the filling of welded joints.Ar/He(CO2) mixtures have been successfully used for the welding of super duplex stainless steels.
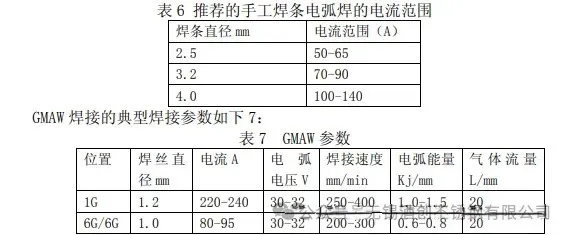
Filling of joints by submerged arc welding is a very practical method of filling joints with 1) material thicknesses of more than 15-20 mm, 2) pipe and vessel diameters of more than 150 mm, and 3) ring and longitudinal joints that can be welded in a flat welding position. The welding of longitudinal and circumferential joints can be carried out in a flat welding position.

V. Duplex stainless steel and dissimilar metal welding
Duplex stainless steels can be welded with other duplex stainless steels, austenitic stainless steels and carbon and low alloy steels. The filler metals of duplex stainless steels have a higher nickel content than the base material and are the most commonly used filler materials for welding duplex stainless steels to other duplex pole metals. When welding with austenitic stainless steels, austenitic filler metals with low carbon and a certain amount of molybdenum will be used for welding duplex stainless steels with austenitic stainless steels; e.g., E309MoL/ER309Lmo; the same filler metals or e.g., E309L/ER309L are commonly used for joining duplex stainless steels to mild and low alloy steel joints. The selection of materials for welding duplex steels to dissimilar steels is shown in the table below .
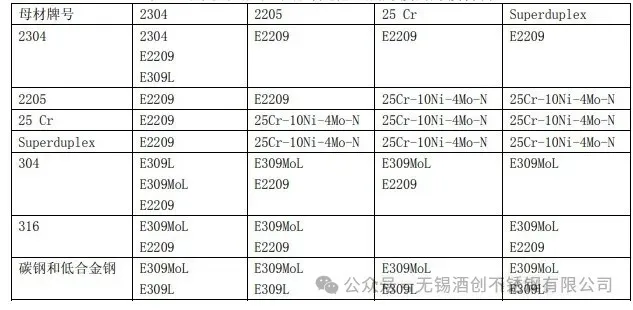
VI. Duplex stainless steel performance evaluation
1. Welding process evaluation
Welding process evaluation according to NB47014, the average tensile strength of up to 782MPa, plastic fracture in the heat-affected zone; 4 side bending specimens without cracks.
2. Phase ratio assessment
Metallographic observation of the organization is a white austenitic matrix distributed with light gray bars and masses of ferrite. The ferrite content of the weld was evaluated to be about 30%; 50%~60% in the heat-affected zone; and 40%~45% in the base metal.
VII.Standardized test method for intermetallic undesirable chemosynthetic phases of duplex stainless steels
Standard test methods for intermetallic undesirable chemosynthetic phases of austenitic-ferritic duplex stainless steels include:
1 Test Method A - Sodium hydroxide etching test for classification of diphase stainless steel etching organization.
2 Test method B - Charpy impact test for classification of duplex steel organizations.
3 Test Method C - Ferric chloride corrosion test for classification of duplex steel organizations.
These test methods detect the presence of intermetallic phases in duplex steels and determine whether the intermetallic phases are present to such an extent that they significantly affect the toughness and corrosion resistance of the material. These test methods may not always detect a reduction in toughness and corrosion resistance due to other causes.
Duplex (austenitic-ferritic) stainless steels are susceptible to the formation of intermetallic compounds when they are in the temperature range of 600 to 1750°F (320 to 955°C). The rate of generation of these precipitated phases is determined by a combination of the chemical composition of each single phase and thermal or thermodynamic processes. The presence of these phases is detrimental to the toughness and corrosion resistance of the material. Proper heat treatment of duplex stainless steels eliminates these undesirable chemosynthetic phases. Rapid cooling of the sample by subsequent heat treatment minimizes the formation of undesirable chemosynthetic phases.
VIII. Duplex stainless steel heat treatment
If necessary, the duplex stainless steel solution treatment. The use of filler wires with high Ni content, making the weld metal Ni content correspondingly higher, intermetallic compounds have the possibility of accelerated precipitation, so according to the ASTM standard duplex stainless steel post-weld heat treatment program recommended specifications for the welded joints solid solution treatment, solid solution temperature of 1070 ° C, holding time of 30 minutes, and then more than 25 ° C / s cooling rate of rapid water cooling. After solid solution of the welded joints for mechanical properties, pitting corrosion resistance test, and metallographic organization observation and ferrite and austenite phase ratio measurement.
IX. Duplex stainless steel summary
The use of suitable welding materials and welding methods, control of moderate welding line energy, is the key to obtain a balanced duplex organization, is the mechanical properties of welded joints and corrosion resistance to ensure the key.
In terms of post-weld testing, appearance inspection, non-destructive testing and mechanical property testing are mainly carried out. Appearance inspection ensures that the surface of the weld is free of defects such as cracks and porosity; non-destructive testing further detects defects within the weld, such as inclusions and unfused joints. Mechanical property tests are used to assess the properties of welded joints such as strength and toughness. Through these strict control and testing measures, we can ensure that the quality and performance of duplex stainless steel welded joints meet the use requirements.
Note: 1. This article refers to some Baidu photos and literature. If there is any infringement, please contact this site to delete, thank you!